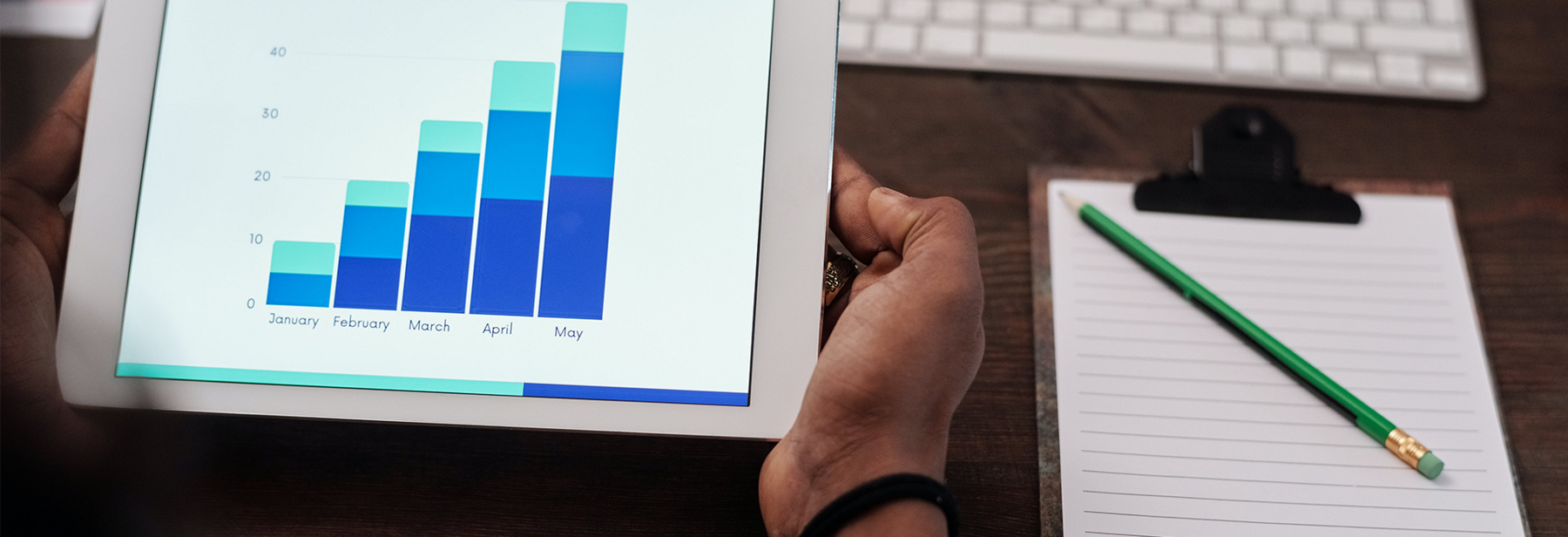
Service in a Time of Rapid Change Series: Supply – The Long Pole in the Tent
– Written by Elizabeth Farquhar for the Center for Services Leadership
Emergency response is nothing new to National Industries for the Blind (NIB).
NIB, the nation’s largest employment resource for those who are blind, provides work to 6,000 people who are blind, including many veterans. It is one of the three central nonprofit agencies designated to administer the U.S. AbilityOne® Program. Jon Katz is vice president of business development, channel management and retail for NIB and serves on the Center for Services Leadership board. He explains this means the government is required by law to purchase from an AbilityOne agency if that agency produces goods or services the government needs.
Delivering during normal times requires highly sophisticated supply chains, Katz explains, but the mandate also extends to periods of disruption, such as war and natural disasters. When the military fights, a hurricane strikes or a river system rises above its banks, NIB must ramp up quickly while maintaining its balance so that it can fulfill the needs of its other customers.
With its extensive experience operating in times of uncertainty, including previous national emergencies, NIB appears distinctly prepared for COVID-19. But this latest virus is posing more and different issues than past crises.
“Like other American manufacturers, we were not immune to the challenges of this unprecedented crisis,” Katz says. The COVID-19 difference is that the exponentially high demand is focused on the same finished goods, and delivery times are dramatically shortened. “Customers want more, and they want it now,” he says. As a result, producers are locked in a similarly competitive position as they struggle to acquire the necessary raw materials.
NIB agencies are flexing to meet the challenge. Like other businesses they have added shifts, extended hours, augmented production lines and equipment and hired more employees. But NIB has had to grapple with other challenges unique to its employee base. Interruptions in public transportation, for example, are especially difficult for those who cannot see and for whom driving is not an option. Layered on top of it all is the need to stop work frequently to deep clean.
NIB agencies are stepping up by shifting focus to markets where the need is greatest. Katz explains that many of the agencies are specialized, but they’ve been able to adapt operationally because of their skills, equipment and local business partnerships. An agency in Binghamton, N.Y. is partnering with a local plastics supplier to make face shields. An agency in San Antonio, Texas has deployed its expert sewers to make thousands of facemasks a week. A Milwaukee, Wis., agency that makes construction kits for the U.S. Army has altered the kits for the National Guard to use in building temporary hospitals. An Orlando call center is now helping to handle Florida’s unemployment claims.
“Communication and transparency are key operating principles in any crisis situation,” Katz says. “It helps organizations maintain trust with its employees, business partners, customers and other stakeholders.”
But securing supplies of raw materials has been the most intractable problem, Katz reports, exposing the risks inherent in global supply chains. Certain supplies and manufacturing should come back onshore, he says.
“The most limiting factor has been the supply of raw materials,” he says. “We found out that in most cases, agencies had the ability to handle the surge, but what we don’t have is that ready access to raw materials. We’re competing with large companies for those materials. It’s the long pole in the tent.